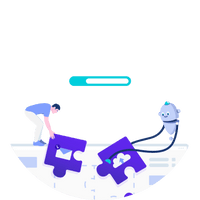
Let's start by saying the obvious: Robotic Process Automation significantly improves efficiency in the logistics industry and supply chains. Both are critical for the global markets, so the robotization case has its weight. More so, software robots influence the evolution of modern commodity trading and RPA technology itself.
Especially these days. Significant events the business has faced since 2019, like the pandemic and war in Ukraine (2022), remind us of the ancient Chinese course "May you live in interesting times." And they are! We see the changes and disturbances in raw materials and goods supplies, trade relations, and market demands.
All those challenges raise a few critical questions:
Among the questions, we could even hear voices repeating the widespread belief that RPA automation will drive people out of their jobs.
Looking for answers, we should point out that while all doubts are understandable, repeating the popular opinions do not serve the business well and may set costly traps. Let's take the Chinese course we cited earlier. Its origin is highly debatable, and the sentence isn't a course at all - not in modern times.
The same goes for worries about RPA reducing jobs. Let's not forget that global markets still struggle with a significant labor shortage, which companies will face for many years to come. Moreover, Western and some Eastern societies are aging fast in addition to various geopolitical and economic turmoil.
In the meantime, the RPA market is proliferating! By 2029 it will probably grow about 32,8% compared to its size in 2021. As we can see, it's not about replacing not enough hands to work. On the contrary! Software robots effectively support workforce retention.
Along with the digital transformation, the way we work changes and thus demands on employees. Logistics and supply chain entities need new skills, roles, and responsibilities followed by new organizational structures to build the best customer service and experience and keep the pace. That means the businesses have to fill the technological gaps in their teams.
McKinsey Global Institute suggests that 87% of enterprises aren't ready to address such a challenge. The problem is that the skills of nearly 45% of employees in the described branches are too conventional to meet present and future expectations. And yet, the same source underlines that about 50% of current logistics and supply chain activities could be automated by 2030. If the surveyed experts are correct, jobs in these areas will soon be different.
Why? Because this is where RPA solutions show their true potential. They help employees automate logic-based tasks without technical knowledge or even deep specifics of a business process. Any staff can realize digital, clerical, and time-consuming activities preparing software bots with a low-code or no-code approach. It increases job satisfaction, minimizes potential errors, and saves time and money wasted on repetitive ventures.
An RPA robot designed to input data into a given system may be a fine and straightforward example. Such a script can smoothly transfer data from one system to another. Simultaneously, a specialist initially assigned to this task may focus on more strategic duties.
Looking at modern logistics companies, one of the critical elements of their activities is collecting data - in large amounts. Before processing and analyzing, gathered information requires processing: cleaning, formatting, and preparation. But the data volume alone is challenging, and so is extracting the variables and numbers relevant for a specific purpose.
To illustrate it, let's consider a task in which the employee tries to determine the optimal route for the shipment. The specialist manually researches and chooses the detailed data from various sources, puts it in a suitable format, and uploads the dataset into the database(s). This way, it is possible to conduct a detailed analysis and provide strategic conclusions. It's trivial to say that the process consumes time and effort and has a high-risk error potential.
Having the above in mind, let's not forget about the Internet of Things. IoT devices are now an integral part of the supply chain - from machines in the production lines to data loggers, supporting essential operations and helping maintain quality at every step of the process. And although they provide all the necessary information, it's hard to set communication between them.
It's getting even more complicated if we consider that every stakeholder processes only a part of the information. This situation leads to many problems, including data silos and difficulties in sharing essential information. Such issues require the supply chain's management centralization. It assures clarity and data visibility from sourcing to delivery, often using APIs.
To add even more meanders to the logistics managers' and employees' everyday routine, we should mention the amount of data and work needed to close a sheer international trade transaction. We are talking about processing over 30 documents with over 20 parties. On average, each paper must comply with more than 600 various regulations and a half thousand trade agreements. It's a complicated and time-consuming task, especially if it has to be done manually.
There are also problems with more physical character. Many companies struggle with ineffective operations. For example, one of the issues is the trucks' empty runs. They result in driving long distances without the cargo, spending expensive fuels and time simply moving from point A to B.
The list of challenges and related complexities faced by logistics and supply chain enterprises is too long for a single article. Yet, it is worth repeating that an excellent answer to all issues mentioned so far and many more is Robotic Process Automation.
RPA provides all necessary tools for every employee, manager, team, or department to work with a significant added value, efficiency, and increased ROI. Looking at the needs of modern logistics entities and the supply chain, we can distinguish several areas where the use of software robots will bring measurable benefits, an impulse for further development, and, above all, will help shape the best customer experience.
One of the critical elements in the activities of logistics companies is shipment and scheduling. Their efficient implementation has an indirect and direct impact on customer satisfaction. In this context, RPA bots will help automate identifying, retrieving, and entering the necessary information from email messages - including attachments like bills of lading (BOLs), carrier invoices, and address details - to internal databases and schedules.
In addition, they will send shipping orders and automatically reply to partners' messages, complete the shipping time, fill in the necessary documentation, and manage alerts for employees. All this will accelerate the related processes and limit the need for manual performance.
In other words, RPA bots can plan, update, and monitor all statuses in the company's systems. They can understand and manage requests from incoming messages with attached documents, log jobs, and other files in scheduling software. The same goes for introducing pick-up times on both carriers and especially customer portals.
That also relates to the improved proof of delivery. The robot can import and integrate data sent from the provider's database and GPS track shipments. At the same time, it will provide evidence of delivery to the customer via chosen channels - email, text message, communicator, mobile app, or other. Similarly, RPA can help verify drivers' logs. It can be done across different elements like time clocks, GPS reports, scanned documents, and others.
These are undoubtedly demanding processes. Related information includes, among others, the quantity of a specific product, its location, condition (damage, storage temperature), messages from the warehouse, etc. All data is consolidated within one system, significantly increasing asset management transparency.
Take condition monitoring as an example. Each sensitive shipment requires appropriate storage and transport conditions. A sensitive cargo has to be stored and transported in a strictly defined manner. Otherwise, all entities in the chain will be at a loss.
An intriguing example may be a US company, the world-leading manufacturer of specialized glass. Their half-finished products are produced in the Far East and transported by sea to the US and then by land to their final destination and further production. During the transportation, the shipment travels by ships and trucks. Either way, the glass must stay at a set temperature and humidity, so the material keeps its properties. Both conditions need to be measured every 30 minutes.
Here, the Internet of Things (IoT) comes in handy. It allows to constantly check the local environment and avoid many problems as the company can respond to emergencies in time. The gathered data help identify specific issues and can be helpful in various analyses, simulations, and forecasting.
Having access to such data, the company can use RPA bots to set given thresholds, report discrepancies, or send notes and requests to departments, warehouses, or transportation units. Such possibilities dramatically improve the management of goods, equipment, and supplies, making it highly proactive.
It is difficult to find more tedious, often complicated, and time-consuming tasks than invoicing processes. At least in logistics. It's also a duty that many employees would prefer o avoid.
Meanwhile, RPA technology allows to automatically and thus flawlessly create and accept invoices, together with the necessary documentation. A single bot can do it way faster and deal with a volume of invoices unreachable to any human.
Moreover, filling in various forms and sending updated documents to customers' B2B portals can also be easily scripted.
Generally, logistics and supply chain entities are often associated with large amounts of papers, like already pointed BOLs, invoices, or delivery proofs. Looking for the best way to manage the documentation leads to - let us repeat one more time - robotization. Robots can retrieve demanded data from almost all electronic files. They have no problem identifying nearly any kind of data, yet it depends on their purpose, code, and actual business needs.
A given bot can also be programmed as a chatbot or assistant, making decisions independently. For example, it can automatically send an additional email to a specific contractor.
Customer satisfaction in the logistics sector is a set of many different methodologies, improvements, and results of well-designed processes. And all those elements may be successfully supported and even developed by RPA technology.
In many materials, as in this one, the issue of enabling employees to focus on more strategic tasks is often raised. The work of representatives can be a great example. They handle hundreds of inquiries and requests from current and potential customers and contractors every day. Automating some of the tasks, initially related to documentation and data processing, allows them to focus on improving customer experience with more energy.
It may sound trivial, but as reality shows such an approach can:
Moreover, the use of RPA bots to carry out such tasks can translate into solid savings. 5 hours saved per week could result in reduced costs of even $ 1.5 million per year!
Another thing influencing customer services is how the company handles returns and after-sales operations. RPA robots can service both, but while the first can be automated entirely, the second can generate unstructured data. That means the latter process requires an employee intervention at some point. Nonetheless, automating such activity as much as possible gives the employee time to deliver the context to such information, avoiding potential bottlenecks in the project.
All that translates into a competitive advantage for a stakeholder. What's more, in both cases, data integrity and added value are preserved. All that demonstrates the flexibility offered by today's RPA systems, even if it's not intuitive at first glance.
Of course, the examples and descriptions given so far are merely a scratch on the surface of the vast topic. Needless to say that today's RPA software, available on the market, allows the cooperation and integration of software robots with new technologies and automation systems.
We can say with certainty that the capabilities of today's software robots allow companies to be more innovative. We can see it in the case of multishuttle systems - especially automated storage and retrieval segments. Bots help move goods across ware- and storehouses, reducing risks related to accidents and other employee hazards.
It is possible when RPA is integrated with optical scanners for assortment recognition. Such devices transmit data to other systems managing a given warehouse. The software determines the movement directions for vending machines and vehicles carrying individual goods, camera paths for drones, etc. It's an intriguing connection between automatization and robotization. As far as transporting, packaging, and surveillance machines perform repetitive operations; the RPA solution can support the process and manage the data.
Some enterprises widely use bots in order fulfillment. Picking or selecting a specific element from the closed set of items is a repetitive operation based on information about shipped goods. A robot can handle the task fast and without errors, maintaining communication between automats or, for example, sending guidelines to mobile terminals and voice picking systems operated by employees.
Robotic Process Automation finds its niches of cooperation with new and advanced technologies like AR - augmented reality devices. Smart glasses are slowly becoming more common in warehouses, directing employees around the storage and allowing save time spent on searching for a given good. Robots process and provide data to the devices opening new ways of creating innovative warehouses with increased performance and efficiency.
Many of the above-described RPA solutions and their applications increasingly involve elements related to cognitive automation. It focuses on activities requiring expert knowledge, context, and other factors - including artificial intelligence (AI) and machine learning (ML) - to perform a specific task. In this case, the goal is to replace humans in the decision-making processes or minimize their effort.
At this point, some might say that it will eliminate human labor from future jobs. In fact, in some companies, managers encounter resistance against RPA from employees who fear losing their jobs. It is understandable, yet that way of thinking is somewhat misleading.
We can find an excellent example in US Air Force. Construction and the aerodynamics of the strategic stealth bomber - Northrop B-2 Spirit (flying wing aircraft) - require constant flight correction carried out by a unique computer. Why not by the pilots? The reason is that a human cannot process that amount of information and make dozen and even hundreds of decisions in a split of a second. Not to mention the fact that it would require re-setting the various elements of the aircraft in a comparable time. And yet, the pilots stay the central and the most crucial part of the flying unit.
That is also why flight control uses systems providing essential data in real-time. No human controller would be able to calculate thousands of constantly changing variables needed for efficient and safe air traffic management.
It may be surprising, but this is the very same reason why various RPA systems often engage in cognitive solutions, including artificial intelligence (AI) and machine learning (ML), in the activities we mentioned in all our examples. This way, the bots can:
As we stated in the beginning, RPA automation increases efficiency in the logistics industry and supply chains. And the same time, it significantly:
RPA solutions work alongside the staff. Bots' functionality is far more critical to the logistics and supply chain enterprises than it may look at first glance. For these entities, the speed and efficiency of actions taken are of key importance and ultimately translate into the level of customer satisfaction. For obvious reasons, it translates into developing competitiveness and profitability, and thus require constant improvement of processes for end-to-end services.
That also underlines the necessity to improve and accelerate the analytical and decision-making capabilities through collecting information about business models and internal activities. It allows the company to simultaneously identify potential errors, disruptions, and shortcomings in various business areas.
All that make RPA an inseparable element of today’s and future logistics. In the coming years, we can expect an increasing involvement of software robots in the activities of companies in this sector. The reason is the growing expectations of efficiency and fast changes in global supply chains.
More information on the widely understood RPA automation is available on our blog.